The GDS Provides a basic setup for performing gearbox experiments and for learning vibration signatures of gearbox and bearing malfunctions. However a detailed investigation of particular and more advance vibration phenomena will acquire additional attachments and fixtures which are available through optional kits. |
Bearing Fault Kit (G-BFK-1)
|
- Learn waveform and spectra of classic bearing defects.
- Learn about signal processing issues such as averaging techniques, leakage, and spectral resolution on determining bearing faults.
- Perform experiments with increasing severity of defects.
- Determine why an ultra-high resolution spectrum is needed to diagnose a bearing fault when fault frequencies are located close to multiples rotational speed.
- Learn how a large signal can mask adjoining low amplitude signal due to spectra leakage.
- The kit consists of one inner race defect, one outer race defect, one with ball defect, and one combination of defects.
|
 |
Defective spur gears (G-SDG)
|
- Study the effect of damaged tooth in gearboxes.
- Apply phase demodulation signal analysis to detect gear damage.
- Investigate backlash between mating gears.
- The kit consists of one missing tooth gear, one chipped tooth gear, one root crack gear, and one surface wear gear
|
 |
Helical gears set (G-HG)
|
- Study the helical gears parallel shaft gearbox.
- Compare vibration signature between spur and helical gears.
- The kit consists of four helical gears to replace standard spur gears in gearbox
|
 |
Defective helical gears (G-HDG)
|
- Study the effect of damaged helical gears.
- Apply phase demodulation signal analysis to detect gear damage.
- The kit consists of one gear with chipped tooth and one gear with missing tooth,and one gear with surface defect
- Requires G-HG
|
 |
Eccentric Spur Gear (G-ESG)
|
- Study the effects of eccentric spur gear.
- Measure the vibration signature of eccentric gears.
- The kit consists of one eccentric spur gear.
|
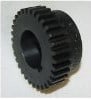 |
Shaft encoder (G-ENC)
|
- Measure transmission error in the gearbox by comparing input and output rotation.
- The kit consists of one 360 pulse per revolution encoder and once per revolution index
|
 |
PC Motor Control Kit (G-PCK)
|
- Operate DDS from remote location.
- Pre-program speed acceleration, deceleration, and length of run to meet exact requirements.
- The kit consists of PC software, one interface module to motor drive and cables.
|
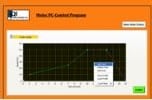 |
PC Load Control Kit (G-PCLK)
|
- Operate magnetic brake from remote location.
- Pre-program load profiles of run to meet exact requirements.
- The kit consists of PC software, one interface module to magnetic brake and cables.
|
|
AC Motor With Built-In Rotor Unbalance (G-UBM)
|
- Study the effects of unbalanced rotor on vibration and/or current signature.
- Study the effect of unbalance rotor on power quality and consumption.
- Study the effect of temperature rise on non-linear characteristics of induction motors.
- The kit consists of one unbalanced 1HP AC motor
|
|
AC Motor With Built-In Rotor Misalignment System (G-MAM)
|
- Study the effect of variable air gap on vibration and/or current signature.
- Study the effect of amount/type of misalignment and rotor speed on vibration/current spectra.
- Determine the effect of misalignment on power quality and consumption.
- Study the effect of temperature rise on non-linear characteristics of induction motors.
- The kit consists of one 1 HP AC motor with custom machined end bells, which allows for easy introduction of known misalignment at either end of the motor.
|
|
AC Motor With Built-In Bowed Rotor (G-BRM)
|
- Study the effects of rotor bow on vibration and/or current signature.
- Study the effect of bowed rotor on power quality and consumption.
- The kit consists of one 1HP AC motor with centrally bent rotor
|
|
AC Motor With Built-In Faulted Bearings (G-FBM)
|
- Study the effects of bearing faults on vibration and/or current signature.
- Study the effect of bearing faults on power quality and consumption.
- The kit consists of one 1 HP AC motor fitted with one inner race faulted bearing and one with outer race faulted bearing. User can specify the types of bearing faults.
|
|
AC Motor With Built-In Broken Rotor Bars (G-BRBM)
|
- Study the effect of broken rotor bars on motor vibration and/or current signature as a function of speed and load.
- Study the effect of broken rotor bars on power quality and consumption.
- Study the effect of temperature rise on non-linear characteristics of induction motors.
- The kit consists of one 1 HP AC motor with broken rotor bars
|
|
AC Motor With Stator Winding Faults (G-SSTM)
|
- Study the effects of turn-to-turn short in stator windings on vibration and/or current signature.
- Study the effect of turn-to-turn short in stator windings on power quality and consumption.
- Study the effect of temperature rise on non-linear characteristics of induction motors.
- The kit consists of one 1 HP AC motor with shorted stator winding turns, and one control box to vary short conditions.
|
|
AC Motor With Voltage Unbalance & Single Phasing (G-VUSM)
|
- Study the effects of voltage unbalance and one phase loss on motor current/vibration signatures.
- Study the effect of voltage unbalance and one phase loss on power quality and consumption.
- Study the effect of temperature rise on non-linear characteristics of induction motors
- The kit consists of one 1 HP AC motor and one control box to vary voltage balance and to disconnect one phase.
|
|